سطح هر ممبران اسمز معکوس (RO) در معرض فولینگ (Fouling) ناشی از مواد خارجی موجود در آب تغذیه مانند هیدراتهای اکسیدهای فلزی، رسوبات کلسیم، مواد آلی و معدنی است. عبارت فولینگ تمامی لایههایی که روی ممبران قرار میگیرد مانند رسوب (Scaling) را شامل میشود. اساسا پیش تصفیه (پیش از ورود به ممبران اسمزمعکوس)، برای کاهش حداکثری آلودگی سطح ممبران طراحی میشود. نصب یک سیستم پیش تصفیه مناسب همراه با انتخاب شرایط بهینه عملیاتی مانند دبی جریان تصفیه شده، فشار و نرخ ریکاوری منجر به کاهش ایجاد آلودگی بر سطح ممبران میگردد.
معمولا فولینگ بر سطح ممبرینها بر اثر عوامل زیر ایجاد میشود:
• سیستم پیش تصفیه ناکافی
• پیش تصفیه تشدید کننده شرایط
• خرابی سیستم دوزینگ مواد شیمیایی
• فلاشینگ (شستشو) ناکافی پس از خاموشی سیستم
• کنترل نامناسب شرایط عملیاتی
• تغییر در ترکیبات آب تغذیه
• تجمع آهسته رسوبات در مدت زمانهای طولانی (باریم و سیلیس)
• آلودگی بیولوژیکی آب تغذیه
فولینگ بر سطح ممبران عموما خودش را به صورت کاهش عملکرد و راندمان سیستم مانند کاهش جریان آب تصفیه شده و/یا افزایش جریان پساب نشان میدهد.
با توجه به مقاومت ممبرانها و اجزای آنها به دما و ثبات pH، فرایند تمیزسازی میتواند به صورت موثری انجام شود. با این وجود باید توجه داشت در صورتی که فرایند تمیزسازی دیر انجام شود، ممکن است که حذف کامل رسوبات از سطح ممبران سخت گردد. در صورتی که فرایند تمیزسازی برای مشکل یک رسوب خاص طراحی شده باشد، موثرتر خواهد بود. گاهی اوقات انتخاب یک ماده شیمیایی اشتباه جهت تمیزسازی میتواند منجر به بدتر شدن شرایط گردد. بنابراین، پیش از تمیزسازی باید نوع رسوب تشخیص داده شود. روشهای مختلفی برای این کار وجود دارد که عبارتند از:
• آنالیز دادههای عملکردی
• تجریه و تحلیل آب تغذیه (یک فولینگ احتمالی ممکن است در آب تغذیه قابل مشاهده و تشخیص باشد)
• بررسی نتایج تمیزسازیهای پیشین
• آنالیز رسوبات چسبیده به فیلتر ممبران مورد استفاده در محاسبه SDI
• آنالیز رسوبات موجود بر روی فیلتر کارتریج
• آنالیز سطح داخلی لوله آب تغذیه (در صورتی که به رنگ قرمز-قهوهای باشد، احتمالا بیانگر حضو رسوبات آهن است؛ رسوبات آلی یا بیولوژیکی عمدتا به صورت لزج یا ژلاتینی می باشند)
الزامات فرایند تمیزسازی
در یک عملیات نرمال، ممبرانهای اسمزمعکوس میتوانند بر اثر رسوبات معدنی، مواد بیولوژیکی، ذرات کلوییدی و مواد آلی غیر محلول دچار فولینگ شوند. این رسوبات در طول عملکرد به تدریج بر سطح ممبران تجمع پیدا میکنند و منجر به افت در دبی جریان تصفیه شده نرمال، افت در میزان دفع نمک نرمال یا هردوی آنها میشوند. درصورت وجود یکی یا بیشتر از موارد زیر، نیاز است که ممبران شستشو داده شود:
• افت 10 درصدی دبی جریان تصفیه شده نرمال
• افزایش 5 تا 10 درصدی دفع نمک نرمال
• افزایش 10 تا 15 درصدی افت فشار نرمال (فشار آب تغذیه منهای فشار جریان پساب)
درصورتی که برای انجام فرایند تمیزسازی زیادی تاخیر کنید، ممکن است که ممبران به صورت کامل تمیز نشود و عملکردش به حالت اولیه برنگردد. همچنین، زمان بین تمیزسازیها کاهش یابد زیرا ممبران با سرعت بیشتری دچار رسوب میشود.
باید توجه داشت که اختلال در پیش تصفیه، کنترل فشار و یا افزایش نرخ ریکاوری نیز میتوانند منجر به کاهش خروجی آب تصفیه شده یا افزایش پساب شوند. درصورتی که چنین مشکلی مشاهده شد، ابتدا باید این علتها را مورد بررسی قرار داد زیرا ممکن است که ممبرانها نیازی به تمیزسازی نداشته باشند. از این رو کمپانی DuPont نرم افزاری به نام FTNORM را طراحی کرده است که برای نرمال سازی دادههای عملکردی ممبرانهای فیلمتک مناسب می باشد. این نرم افزار کمک میکند تا زمان دقیق تمیزسازی ممبران به درستی تشخیص داده شود. نرم افزار FTNORM را میتوانید از سایت کمپانی دوپونت دانلود کنید.
تجهیزات موردنیاز تمیزسازی
در تصویر زیر تجهیزات موردنیاز جهت فرایند تمیزسازی نمایش داده شده است. pH محلول تمیز سازی مورد استفاده میتواند در محدوده 1 تا 13 باشد؛ بنابراین تجهیزات تمیزسازی باید از مواد مقاوم در برابر خوردگی ساخته شوند.
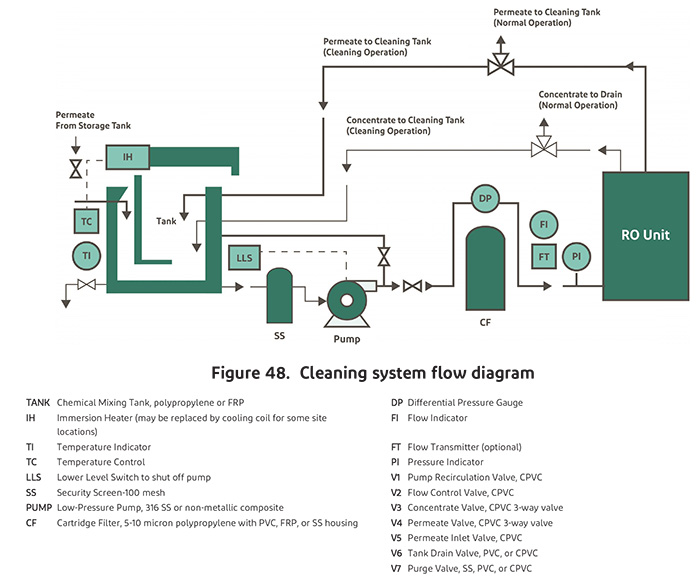
باید توجه داشت که مخزن اختلاط باید از پلیپروپیلن یا FRP ساخته شود و دارای یک پوشش قابل جدا شدن و گیج دما باشد. همچنین با توجه به این که فرایند تمیزسازی در دمای گرم، تاثیر بیشتری دارد، پیشنهاد میشود که دما و pH محلول تمیزسازی مطابق دستورالعملهای ممبرانها باشد. توصیه میشود دمای محلول تمیزسازی کمتر از 20 نباشد زیرا در دماهای پایین سینتیک مواد شیمیایی بسیار کند است. همچنین برخی مواد مانند سدیم لوریل سولفات در دماهای پایین ممکن است رسوب کنند. در برخی مناطق جغرافیایی ممکن است به سیستم خنک کننده نیز نیاز باشد. بنابراین هر دو سیستم گرمایشی و سرمایشی باید در طراحی سیستم تمیزسازی در نظر گرفته شوند.
یک قانون سرانگشتی برای محاسبه سایز تانک تمیزسازی این است که حجم پرشروسلهای خالی را با حجم لولههای تغذیه و برگشتی جمع کرد. برای مثال برای تمیزسازی پرشروسلهای 8 اینچی که دارای 6 المان در هر وسل هستند، محاسبات زیر را باید انجام داد:
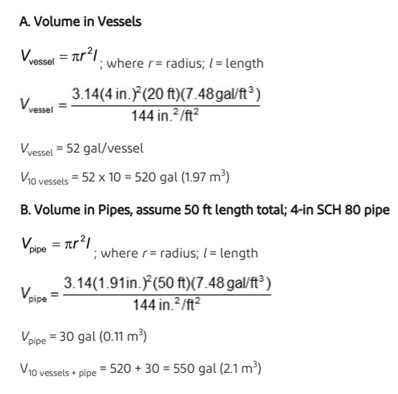
درنتیجه حجم تانک ذخیره سازی باید 550 گالن در نظر گرفته شود.
پمپ تمیزسازی نیز باید با توجه به فشارها و دبیهای ذکر شده در جدول زیر انتخاب شود. همچنین پمپ باید از جنس SS316 و یا کامپوزیتهای غیرفلزی انتخاب شود.
جدول شماره 1
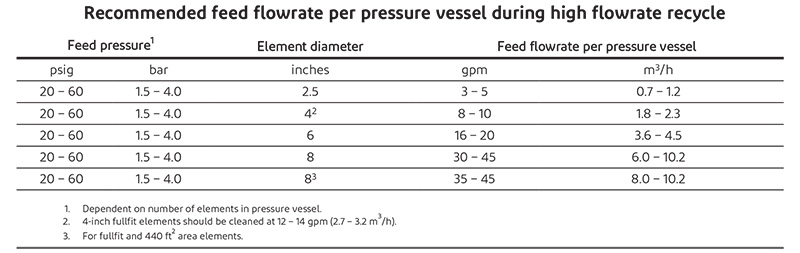
همچنین برای کنترل درست جریان از شیرها، فلومترها و فشارسنجهای مناسب باید استفاده شود و دبی جریان همواره باید به طور متوسط 10 فوت بر ثانیه (3 متر بر ثانیه) یا کمتر باشد.
مراحل تمیزسازی
برای تمیزسازی ممبرانهای اسمزمعکوس 6 گام وجود دارد:
1. آماده سازی محلول تمیزسازی
2. پمپاژ با جریان کم: محلول تمیزسازی مخلوط شده و از قبل گرم شده را در شرایط دبی کم جریان (حدود نصف مقادیر جدول 1) و فشار کم برای جابجایی آب فرایند به وسل پمپ کنید. فقط از فشار کافی جهت جبران افت فشار از جریان تغذیه به جریان تغلیظ شده استفاده کنید. فشار باید به حدی کم باشد که تقریبا هیچ آب تصفیه شدهای تولید نشود. فشار کم، نشستن مجدد آلودگیها بر سطح ممبران را به حداقل میرساند. در صورت لزوم جریان تغلیظ شده را تخلیه کنید تا از رقیق شدن محلول تمیزسازی جلوگیری گردد.
3. بازچرخش: پس از جابجایی آب فرایند، محلول تمیزکننده در جریان تغلیظ شده وجود خواهد داشت. سپس جریان تغلیظ شده و جریان تصفیه شده را به مخزن محلول تمیزسازی بازچرخش کنید و اجازه دهید دما تثبیت شود. pH محلول را اندازه گیری کنید و در صورت نیاز آن را تنظیم کنید.
4. خیس خوردن: پمپ را خاموش کنید و به المانها اجازه دهید تا خیس بخورند. برخی اوقات خیس خوردگی به مدت یک ساعت کافی است. برای فولینگهای سخت، زمان خیس خوردگی بیشتر سودمند است؛ از این رو المانها را یک شب به مدت 10 تا 15 ساعت خیس کنید. برای حفظ دمای بالا در طول خیس خوردگی طولانی، از سرعت چرخش آهسته (حدود 10% مقادیر جدول 1) استفاده کنید.
5. پمپاژ با جریان بالا: محلول تمیز کننده را برای مدت 30 الی 60 دقیقه به عنوان جریان تغذیه با سرعتهای ذکر شده در جدول 1 به سیستم وارد کنید. دبی بالا باعث شستشوی رسوباتی که با محلول تمیز سازی از سطح ممبران جدا شدهاند، میشود. در صورتی که المانها به شدت رسوب کرده باشند، نیاز است که از دبی 50 درصد بیشتر نسبت به مقادیر جدول 1 استفاده شود. در دبیهای بالاتر، افت فشار بیشتر ممکن است که مشکل ساز باشد. حداکثر افت فشار برای هر المان 15psi یا برای وسلهای چند المانه 50psi است، هرکدام که محدود کنندهتر باشد، افت فشار محسوب میشود. باید توجه شود که 15 یا 50 psi نباید به عنوان معیار تمیزسازی در نظر گرفته شود. تمیزسازی زمانی توصیه میشود که افت فشار 15 درصد افزایش یابد. افت فشار بیش از 50psi در یک مرحله ممکن است آسیب قابل توجه در ممبران ایجاد کند.
6. شستشو: توصیه میشود که از آب تصفیه شده توسط ممبران RO یا آب دیونیزه جهت شستشو استفاده شود. آب خام پیش تصفیه شده یا آب تغذیه نباید مورد استفاده قرار گیرد زیرا ترکیبات موجود در آنها ممکن است که با محلول تمیزسازی واکنش دهند و رسوب بر روی سطح ممبران ایجاد کنند. حداقل دمای آب شستشو باید 20 درجه سلسیوس باشد.
نکات مهم در تمیزسازی ممبرانها
1. اکیدا توصیه میشود که تمامی مراحل سیستمهای RO جداگانه تمیزسازی شوند. این امر علاوه بر این که مانع از هل دادن رسوبات جدا شده از مرحله اول به مرحله دوم میشود؛ از کم شدن راندمان تمیزسازی نیز جلوگیری میکند. در صورتی که سیستم از 3 مرحله ایجاد شده باشد. مراحل 2 و 3 باید جداگانه تمیز شوند. برای سیستمهای چند مرحلهای، اگرچه هر مرحله باید به صورت جداگانه تمیز شود؛ اما ممکن است که عملیات شستشو و خیس خوردگی به صورت همزمان در تمامی مراحل صورت گیرد. هنگامی که محلول تمیزسازی کدر شد و یا تغییر رنگ داد، نیاز است که محلول تمیزسازی جدید آماده شود. با توجه به این که گردش مجدد با جریان بالا باید به صورت جداگانه برای هر مرحله اعمال گردد، دبی جریان نباید در مرحله اول خیلی کم یا در مرحله آخر خیلی زیاد باشد. این کار را میتوان با یک پمپ تمیزسازی و انجام هر مرحله در یک زمان و یا با استفاده از چندین پمپ تمیزسازی برای هر مرحله انجام داد.
2. فولینگ یا اسکیلینگ المانها معمولا ترکیبی از چندین رسوب است. برای مثال ترکیبی از فولینگ آلی، فولینگ کلوییدی و بیوفولینگ همزمان وجود دارد. بنابراین بسیار مهم است که مرحله اول تمیزسازی به درستی انتخاب گردد. کمپانی فیلمتک پیشنهاد میدهد که تمیزسازی قلیایی به عنوان مرحله اول انتخاب شود. تمیزسازی اسیدی تنها زمانی به عنوان مرحله اول انتخاب میگردد که فقط کلسیم کربنات یا اکسید/هیدورکسید آهن در سطح ممبرانها حضور دارد.
تمیزکنندههای اسیدی عمدتا با سلیس، مواد آلی (مثلا اسید هیومیک) و بیوفیلم موجود در سطح ممبران واکنش میدهند و این امر ممکن است باعث کاهش بیشتر راندمان ممبران گردد. برخی اوقات، تمیزسازی قلیایی، ممکن است این افت ناشی از تمیزسازی اسیدی را جبران کند اما اغلب یک تمیزسازی شدید ضروری میباشد. تمیزسازی شدید در pH و دمایی که خارج از دستورالعملهای سازنده است و یا با موادی که با ممبرانها سازگار نیستند، انجام میشود. تمیزسازی شدید فقظ باید به عنوان آخرین راهکار استفاده شود زیرا ممکن است که به ممبران آسیب وارد کند.
در صورتی که سیستم RO دارای رسوبات کلوییدی، آلی یا بیولوژیکی همراه با کلسیم کربنات باشد، تمیزسازی دو مرحلهای نیاز است؛ به صورتی که ابتدا تمیزسازی قلیایی و سپس تمیزسازی اسیدی. تمیزسازی اسیدی زمانی انجام میشود که تمیزسازی قلیایی به صورت موثری فولینگهای آلی، کلوییدی و بیوفولینگ را حذف کرده باشد.
3. در طول تمیزسازی همواره pH را اندازه گیری کنید. در صورتی که در هنگام تمیزسازی اسیدی، pH بیش از 0.5 واحد افزایش یابد، اسید بیشتری نیاز است که افزوده شود. همچنین اگر در هنگام تمیزسازی قلیایی، pH بیش از 0.5 واحد کاهش یابد، سود بیشتری باید افزوده شود.
4. در صورتی که زمان خیس خوردگی طولانی باشد، این امکان برای محلول وجود دارد که به صورت کامل اشباع شود و رسوبات دوباره به سطح ممبران برگردند. همچنین، در طول این مدت دما نیز کاهش مییابد، بنابراین، اثر خیس خوردگی کم می شود. پیشنهاد میشود که محلول را به صورت مداوم بچرخانید تا دما حفظ شود (دما نباید بیش از 5 درجه کاهش یابد) و در صورت نیاز به تنظیم pH، مواد شیمیایی افزوده گردد.
5. محلولهای تمیزسازی کدر یا به شدت رنگی باید جایگزین شوند و عملیات تمیزسازی با یک محلول تازه تکرار شود.
6. در صورتی که سیستم به مدت 24 ساعت یا بیشتر باید خاموش شود، ممبرانها باید در محلول 1% وزنی متابیسولفیت سدیم ذخیره گردند.
تاثیر pH بر حذف رسوبات
علاوه بر انتخاب توالی درست تمیزسازی (ابتدا تمیزسازی قلیایی)، انتخاب pH درست نیز برای حذف بهینه رسوبات ضروری است. درصورتی که رسوبات با موفقیت حذف نشوند، عملکرد سیستم ممبرانها با سرعت بیشتری کاهش مییابد زیرا برای مواد رسوب کننده راحتتر است تا بر سطح ممبران رسوب کنند. همچنین، زمان بین تمیزسازیها کاهش مییابد و منجر به کاهش طول عمر ممبران و افزایش هزینههای عملیاتی و نگهداری میشود.
فرایند تمیزسازی موثر منجر به طولانیتر شدن زمان عملیات بین تمیزسازیها میشود؛ همچنین هزینه های عملیاتی را کاهش میدهد.
در تصویرهای زیر اهمیت انتخاب pH مناسب برای تمیزسازی درست ممبرانها نمایش داده شده است.
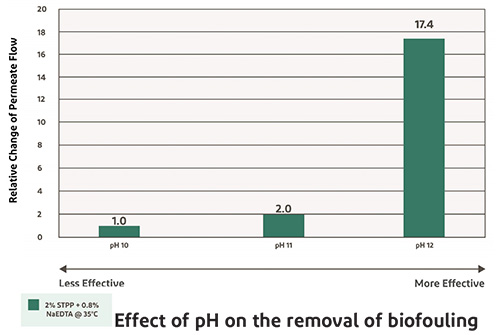
همانطور که مشاهده میشود، رسوبات کلسیم کربنات با تمیزسازی با هیدروکلریک اسید در pH حدود 1-2 بیشترین حذف را دارند، درحالی که بیشترین حذف رسوبات بیولوژیکی (بیوفولینگها) در pH برابر 12 است.
مواد شیمیایی تمیزسازی
در جدول زیر لیست مواد شیمیایی مناسب تمیزسازی ممبرانها نمایش داده شده است. تمیز کنندههای اسیدی و قلیایی جزو مواد شیمیایی تمیز کننده استاندارد محسوب میشوند. تمیز کنندههای اسیدی، برای حذف رسوبات غیرآلی مانند آهن مناسب هستند، درحالی که تمیز کنندههای قلیایی برای حذف رسوبات آلی شامل مواد بیولوژیکی استفاده میشوند. در فرایند تمیزسازی نباید از سولفوریک اسید استفاده شود زیرا احتمال تشکیل رسوبات کلسیم سولفات وجود دارد. همچنین لازم به ذکر است که برای آماده سازی محلولهای تمیزسازی از آب تصفیه شده توسط RO یا آب دیونیزه باید استفاده گردد.
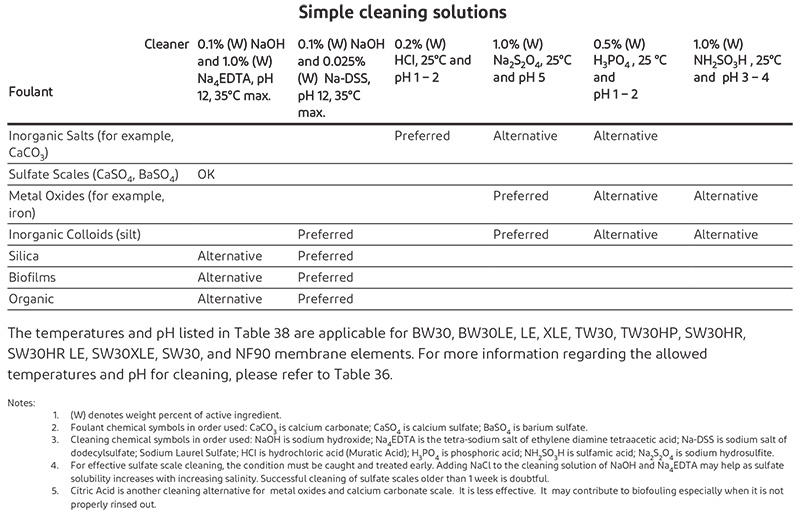
فرایند تمیزسازی برای شرایط خاص
هر فرایند تمیزسازی با توجه به نوع رسوبات موجود بر سطح ممبران متفاوت است و به توصیههای خاص خودش نیاز دارد. برای کسب اطلاعاتی که در همه موارد تمیزسازی مشابه هستند مانند تجهیزات، دبی جریان، محدودیتهای pH و دما به دستورالعملهای کلی تمیز سازی مراجعه کنید و سپس در صورت نیاز توصیههای خاص را اعمال کنید.
رسوب سولفات
روند تمیزسازی زیر به طور خاص برای سیستمهایی طراحی شده است که دچار رسوب سولفات بر روی المانها شده اند. تمیزسازی رسوبات سولفات بسیار سخت است. در صورتی که این رسوبات زود تشخیص داده نشوند، احتمال موفقیت فرایند تمیزسازی بسیار کم می باشد و به احتمال زیاد، افت جریان رخ خواهد داد که قابل جبران نیست. برای بازیابی عملکرد سیستم غشایی، ممکن است چندین دوره تمیزسازی و خیس خوردگی نیاز باشد.
روند تمیزسازی رسوبات سولفات به شرح زیر است و دارای 7 گام میباشد:
1. آماده سازی محلول تمیزسازی مطابق جدول زیر
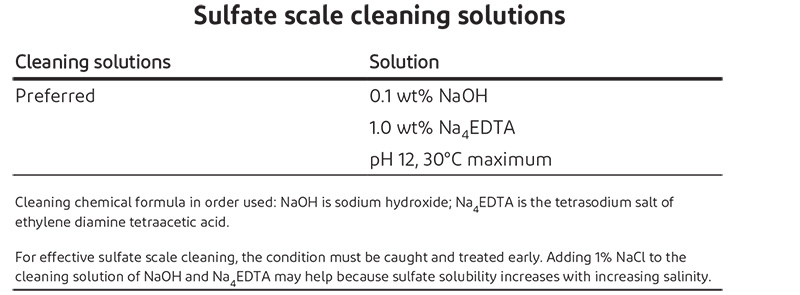
2. ورود محلول تمیز سازی به سیستم
3. بازچرخش محلول تمیزسازی به مدت 30 دقیقه
4. خیس خوردن ممبرانها در محلول تمیزسازی برای مدت 1 تا 15 ساعت
5. پمپاژ با جریان بالا
6. شستشو
7. راه اندازی مجدد
رسوب کربنات
روش تمیزسازی زیر به طور خاص برای سیستمهایی طراحی شده است که رسوبات کربنات بر سطح ممبرانهایشان قرار گرفته است. هنگامی که رسوبات کلسیم کربنات شدید هستند، دمای محلول تمیزسازی را ممکن است تا بیش از 35 درجه سلسیوس افزایش دهند. تمیزسازی رسوبات کلسیم به طور مرسوم در دمای 20 تا 25 درجه سلسیوس صورت میگیرد. فرایند تمیزسازی زمانی کامل در نظر گرفته میشود که pH محلول تمیزسازی در طول فرایند بازچرخش و یا پمپاژ با جریان بالا تغییر نکند.
برای تمیزسازی رسوبات کربنات 7 گام وجود دارد که عبارتند از:
1. آماده سازی محلول تمیزسازی مطابق جدول زیر
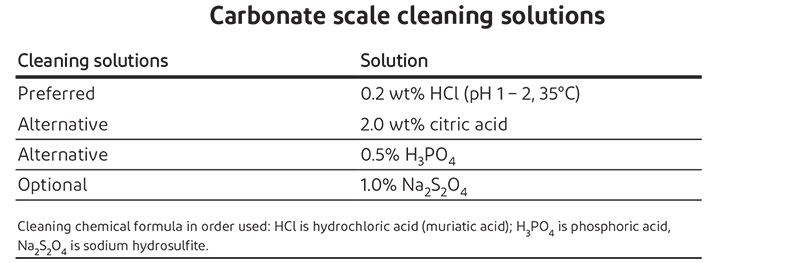
2. ورود محلول تمیز سازی
3. بازچرخش: محلول تمیزسازی را به مدت 10 دقیقه یا تا زمانی که هیچگونه تغییر رنگی مشاهده نشود، بازچرخش کنید. اگر هر زمان در هنگام فرایند چرخش، تغییر رنگ مشاهده شد، محلول را دور ریخته و یک محلول جدید آماده کنید. برای تمیزسازی موثر، pH را نیز ثابت نگه دارید. درصورت نیاز و برای ثابت نگه داشتن pH میتوانید مواد شیمیایی تمیزسازی اضافی را نیز به محلول بیفزایید.
4. خیس خوردگی: برای سیستمهایی با میزان رسوب کم، 1 الی 2 ساعت خیس خوردگی کافی است. سیستمهایی با رسوب شدید را نیز میتوان با زمان خیس خوردگی طولانی احیا کرد. ممبرانهایی با رسوبات شدید را باید به صورت جداگانه، بیرون از پرشروسل و در حالت عمودی خیس نگه داشت. همچنین، pH را نیز چک کنید و در صورت نیاز آن را تنظیم کنید و یا محلول تمیزسازی را تعویض کنید.
5. پمپاژ با جریان بالا
6. شستشو
7. راه اندازی مجدد
رسوب آهن
روش زیر به طور خاص برای سیستمهایی که دچار رسوب آهن شدهاند، مناسب میباشد. فرایند تمیزسازی رسوبات آهن شامل 7 گام زیر است:
1. آماده سازی محلول تمیزسازی مطابق جدول زیر
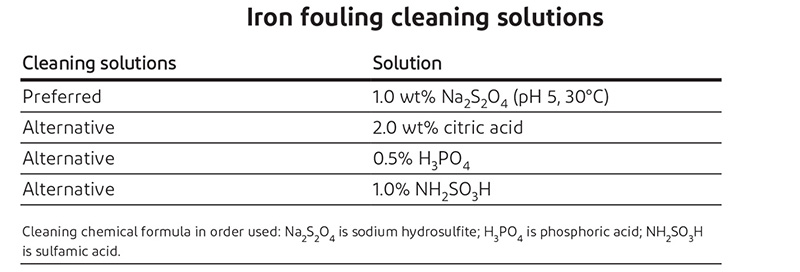
2. ورود محلول تمیزکننده
3. بازچرخش
4. خیس خوردگی: برای این که سدیم هیدروسولفیت اثرگذاری خوبی داشته باشد، خیس خوردگی ضروری است. 2 الی 4 ساعت زمان مرسوم برای خیس خوردگی میباشد اما با توجه به شدت رسوبات، این مدت ممکن است تغییر کند.
5. پمپاژ با جریان بالا
6. شستشو
7. راه اندازی مجدد
لازم به ذکر است که سدیم هیدروسولفیت بوی بسیار تندی دارد، بنابراین اتاق باید به خوبی تهویه شود. همچنین توجه شود که تمامی مقررات و اصول ایمنی رعایت شوند. نکته مهم در موفقیت عملیات تمیزسازی، زمان تماس است. همچنین برخی اوقات در هنگام تمیزسازی، محلول دچار تغییر رنگ میشود و به رنگهای مشکی، قهوهای و زرد درمیآید که تمامی این موارد برای چنین نوعی از تمیزسازی طبیعی است. تنها باید توجه داشت، هنگامی که محلول تمیزسازی تغییر رنگ داد، باید آن را دور ریخت و محلول جدید آماده کرد. مدت زمان و تعداد دورههای خیس خوردگی نیز به شدت رسوبات بستگی دارد.
رسوب مواد آلی
روش تمیزسازی زیر به طور خاص برای سیستمهایی طراحی شده است که دچار رسوبات مواد آلی مانند هیومیک اسیدها، فولیک اسیدها، آنتی اسکالانتها و یا روغنها شدهاند. این روش شامل 8 گام است. در 6 مرحله اولیه، ابتدا تمیزسازی با محلول با pH بالا انجام میشود و سپس این مراحل با محلول تمیزسازی با pH پایین تکرار میشود. 8 مرحله این روش عبارتند از:
1. آماده سازی محلول تمیزسازی با pH بالا مطابق جدول زیر
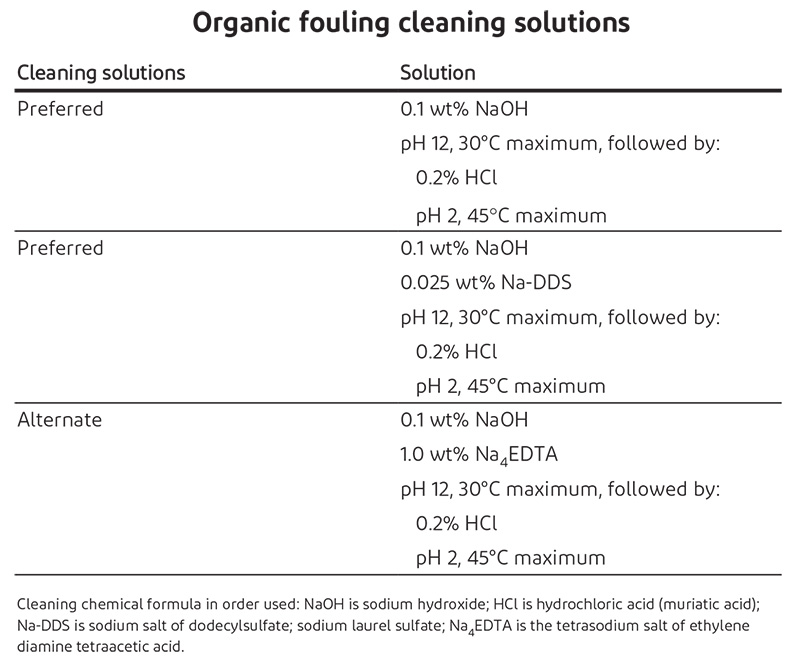
2. ورود محلول تمیز سازی به سیستم
3. بازچرخش محلول تمیزسازی به مدت 30 دقیقه. درصورتی که محلول تغییر رنگ داد، آن را دور بریزید و یک محلول جدید آماده کنید.
4. خیس خوردگی
5. پمپاژ با جریان بالا
6. شستشو
7. تکرار گامهای 2 تا 6 با محلول تمیزسازی HCl در pH برابر 2
8. راه اندازی مجدد
برای تاثیر حداکثری، دمای محلول تمیزسازی باید بیشتر از 25 درجه سلسیوس باشد. بالا بردن دمای محلول تمیزسازی به حذف مواد آلی از سطح ممبران کمک میکند. بعضی از مواد آلی مانند روغنها به سختی پاک میشوند. برای حذف آنها و دستیابی به راندمان بهینه، زمانهای مختلف خیس خوردگی را آزمایش کنید. همچنین، موثرترین محلول تمیزسازی معمولا دارای یک سورفکتانت مانند Na-DDS یا برخی از تمیز کنندههای تجاری حاوی سورفکتانت یا مواد شویندهای که به حذف روغنها کمک میکنند، هستند.
درصورتی که رسوب آلی ناشی از استفاده بیش از اندازه از یک منعقد کننده برای پیش تصفیه آب تغذیه باشد، عوض کردن ترتیب تمیز کنندهها میتواند موثر واقع گردد. برای تعیین ترتیب درست محلولهای تمیزسازی (ابتدا محلول با pH بالا و سپس محلول با pH پایین و یا برعکس)، سعی کنید که نمونهای از رسوب آلی موجود در سیستم خود را جمع آوری کنید؛ سپس نمونه را با دو حالت ابتدا سود سپس اسید و یا ابتدا اسید سپس سود مورد آزمایش قرار دهید تا بتوانید تشخیص دهید که کدام ترتیب استفاده از تمیزکنندهها، رسوبات را بهتر در خود حل میکند.
رسوب بیولوژیکی یا بیوفولینگ
روش تمیزسازی زیر به طور خاص برای سیستمهایی طراحی شده است که با مواد بیولوژیکی دچار رسوب شدهاند. این روش شامل 7 مرحله است که عبارتند از:
1. آماده سازی محلول تمیزسازی مطابق جدول زیر
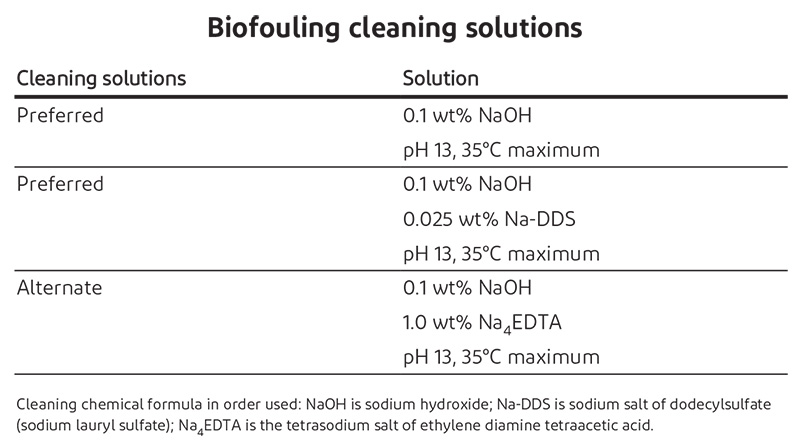
2. ورود محلول تمیزسازی به سیستم
3. بازچرخش
4. خیس خوردگی
5. پمپاژ با جریان بالا
6. شستشو
7. راه اندازی مجدد
تجربه نشان داده است که محلول تمیزسازی Na4EDTA همراه با سود، تاثیر کمتری نسبت به محلول استاندارد سود یا محلول سود همراه با Na-DDS دارد.
برای هر راهکاری، زمان حیاتی است. ممکن است برای بازیابی عملکرد سیستم، چندین شب خیس خوردگی ضروری باشد. پس از این که المانها تمیز شد، بسیار مفید است که یکبار دیگر آخرین لایه بیوفیلم موجود بر سطح ممبران را تمیز کرد. هر بیوفیلم باقی مانده بر سطح ممبران تمایل دارد که آلودگیها را جذب و به دام بیندازد، بنابراین تمیزسازی اضافی منجر به افزایش زمان بین پاکسازیهای ممبرانها میشود. در شرایط بیوفولینگ شدید، ممکن است برای بهبود نتایج تمیزسازی، از یک بیوساید (زیست کش) نیز کمک گرفت. همچنین درصورتی که بیوفولینگ (رسوب زیستی) یک مشکل عملیاتی باشد، ضدعفونی منظم پس از تمیزسازی توصیه میشود.
تمیزسازی اضطراری
درصورتی که تمیزسازی ممبرانها به موقع انجام نشود، به عنوان مثال زمانی بخواهیم تمیز انجام دهیم که اختلاف فشار (ΔP) دو برابر شده باشد یا جریان آب تصفیه شده نرمال تا 50 درصد افت کرده باشد، احتمال موفقیت روشهای پاکسازی ذکرشده محدود میشود. درصورتی که روشهای تمیزسازی استاندارد، نتوانند رسوبات را حذف کنند، نیاز است که از روشهای سختتر و شدیدتری استفاده شود. البته باید توجه داشت که در این شرایط هیچ تضمینی برای عملکرد درست ممبران پس از این پاکسازیها وجود ندارد.
ضدعفونی ممبرانها
سیستمهای غشایی را جهت نگه داشتن مقدار میکروارگانیسمها در محدوده کم، ضدعفونی میکنند. دو دلیل اصلی برای ضرورت ضدغفونی کردن ممبرانها وجود دارد که این دو دلیل عبارتند از:
1. عملکرد هموار: میکروارگانیسمها ممکن است به صورت بیوفیلم بر سطح ممبرانها یا جداکنندههای جریان رشد کنند و منجر به بیوفولینگ یا رسوب زیستی شوند. رسوب زیستی یک تهدید بزرگ برای سیستم است و ضدعفونی منظم یک استراتژی برای کنترل این رسوب میباشد. ضدعفونی منظم باعث میشود که سطح رشد بیولوژیکی پایین نگه داشته شود و از مشکلات عملیاتی جلوگیری گردد. در سیستمهای اسمز معکوسی که با آب تغذیه فعال از نظر بیولوژیکی کار میکنند، بیوفیلم میتواند ظرف 3 تا 5 روز ظاهر شود. بنابراین، تناوب ضدعفونی مرسوم در زمان اوج فعالیت بیولوژیکی (تابستان) هر 3 تا 5 روز و در زمان فعالیت بیولوژیکی کم (زمستان) هر 7 روز است. تعیین زمان بهینه ضدعفونی بهینه برای هر سیستم متفاوت میباشد و باید با توجه به ویژگیهای عملیاتی سیستم RO مشخص گردد.
2. کیفیت آب تصفیه شده: برخی کاربردها مانند صنایع غذایی و دارویی، به آب تصفیه شده با کیفیت بسیار بالا با توجه به شاخصهای میکروبیولوژیکی نیازمندند. ممبرانهای اسمزمعکوس یا نانوفیلتراسیون، به صورت تئوری 100 درصد میکروارگانیسمها را حذف میکنند اما هر نشت کوچکی در سیستم غشایی، ممکن است باعث آلوده شدن آب تصفیه شده گردد. درصورتی که بیوفیلم در آب تغذیه وجود داشته باشد، خطر آلودگی بیشتر است؛ بنابراین، ممبران باید در وضعیت ضدعفونی شده نگه داشته شود. ضدعفونی منظم در این کاربردها برای بهبود کیفیت میکروبیولوژیکی آب تصفیه الزامی است، حتی اگر هیچگونه مشکل عملیاتی وجود نداشته باشد.
ضدعفونی با هیدروژن پراکسید و پراستیک اسید
پراکسید هیدروژن و یا ترکیبی از پراکسید هیدروژن و پراستیک اسید برای تصفیه سیستمهای ممبرانی که دچار آلودگی بیولوژیکی شدهاند، مناسب است. محلولهای غلیظ پراکسید هیدروژن/پراستیک اسید در بازار موجود هستند که میتوان آنها را با آب تصفیه شده توسط RO، مخلوط کرد تا محلول 0.1 درصد وزنی پراکسید ایجاد شود.
دو عامل دما و آهن، بر نرخ حملهی پراکسید هیدروژن بر ممبرین تاثیر شدیدی دارند. دمای محلول ضدعفونی کننده نباید از 25 درجه سلسیوس بیشتر باشد. آزمایش ممبرانهای FT30 با محلول پراکسید هیدروژن 0.5% در دمای 34 درجه سلسیوس، پس از چند ساعت، عبور نمک بالایی را نشان داد. درحالی که همین ممبرانها در دمای 24 درجه با محلول پراکسید هیدروژن 0.5% تا 96 ساعت سازگاری داشتند. حضور آهن یا دیگر فلزات واسطه همراه با محلول هیدروژن پراکسید نیز میتواند منجر به خرابی ممبرانها گردد. ممبرانهای FT30 با محلول پراکسید هیدروژن 0.15% و آب شیر حاوی آهن تست شدند. نتایج نشان داد که پس از 150 ساعت، عبور نمک از ممبرین به مقدار قابل توجهی افزایش یافت. قرار گرفتن دائمی ممبران با این غلظت، درنهایت منجر به خرابی ممبران میگردد، درحالی که استفاده دورهای توصیه میشود.
برای سیستمهای اسمزمعکوس که دچار آلودگی بیولوژیکی شده اند، روش زیر برای استفاده از محلولهای پراکسید هیدروژن توصیه شده است:
1. قبل از ضدعفونی کردن باید هرگونه رسوب روی سطح ممبران یا دیگر بخشهای سیستم را با یک محلول تمیزسازی قلیایی جدا کرد. حذف این رسوبات که میکروارگانیسمها را در خود جای داده اند، باعث به حداکثر رسیدن درجه ضدعفونی میشود. پس از پاکسازی قلیایی، سیستم را با آب تصفیه شده RO شستشو دهید.
2. سیستم را با اسید تمیزسازی کنید (مطابق بخش رسوب آهن) تا تمامی آهنهای موجود بر سطح ممبران حذف شوند؛ سپس سیستم را با آب تصفیه شده توسط RO شستشو دهید.
3. محلول 0.1% وزنی هیدروژن پراکسید رقیق شده با آب تصفیه شده RO با دمای کمتر از 25 درجه سلسیوس را برای مدت 20 دقیقه در سیستم به چرخش درآورید. pH حدود 3 تا 4 بهترین راندمان را دارد و طول عمر ممبران را افزایش میدهد.
4. توصیه میشود که ممبرانها را حداکثر هر 1 الی 2 بار در هفته ضدعفونی کنید.
ضدعفونی با کلر و سایر محصولات زیست کش
استفاده از کلر آزاد، دیاکسید کلر یا زیست کشهایی که دارای کلر ترکیبی هستند، عموما پیشنهاد نمیشود. همچنین ید، بیوسایدهای چهارتایی و ترکیبات فنولی که منجر به افت فشار میشوند نیز به عنوان زیست کش توصیه نمیگردند.
ضدعفونی با حرارت
ممبرانهای سری HSRO فیلمتک که مخفف heat-sanitizable reverse osmosis هستند را میتوان با حرارت دادن ضدعفونی کرد. این روش ضدعفونی سازی انتخابی بسیار عالی برای مصارف غذایی و دارویی است. از مزایای این روش میتوان به موارد زیر اشاره کرد:
• دسترسی احتمالی به مناطقی که مواد شیمیایی نمیتوانند دسترسی داشته باشند.
• اعتبارسنجی ساده
- ساده تر بودن کنترل گرما در مقایسه با غلظت مواد شیمیایی
- آسان تر بودن اثبات پخش کامل گرما
• عدم نیاز به شستشو مواد شیمیایی
• عدم نیاز به ذخیره سازی مواد شیمیایی
• حداقل سازی مشکلات دفع زباله
• عدم نیاز به تایید مواد شیمیایی
ممبرانهای جدید سری HSRO پیش از قرار گرفتن در معرض آب داغ، نیاز به پیش-آماده سازی دارند. قبل از پیش-آماده سازی، ممبرانها باید در آب تغذیه با فشار و دفع نمک کاهش یافته فعالیت کنند. در تمامی مراحل پیش-آماده سازی باید از آب با کیفیت مناسب استفاده شود. این آب فاقد کلر و مواد رسوب کننده است. توصیه میشود که از آب تصفیه شده توسط RO استفاده گردد، اما آب تغذیه پیش تصفیه شده نیز ممکن است مورد استفاده قرار گیرد. یک روش آماده سازی مناسب شامل مراحل زیر است:
1. شستشو جهت زهکشی با آب با کیفیت مناسب (برای مدت 30 دقیقه) در فشار و دبی جریان تصفیه شده کم
2. بازچرخش آب گرم تا زمانی که سیستم گرم شود (تا 45 درجه و کمتر) در فشار خیلی کم (فشار بین غشایی کمتر از 25psi با حداکثر فشار تغذیه 45psi). حداکثر افت فشار در هر تک المان نیز 1.5psi است.
3. ورود آب داغ به سیستم جهت افزایش دما تا 80 درجه سلسیوس. دمای آب را با نرخ بیشتر از 1 الی 2 درجه بر دقیقه (حداکثر 4 درجه بر دقیقه) افزایش ندهید.
4. هنگامی که آب داغ (45 درجه یا بیشتر) به سیستم وارد میشود، فشار بین ممبرانها را کمتر از 25psi نگه دارید.
5. دما را برای مدت 60 تا 90 دقیقه نگه دارید.
6. اجازه دهید که سیستم تا دمای 45 درجه یا کمتر خنک شود. دما را با نرخ بیشتر از 1 الی 2 درجه بر دقیقه (حداکثر 4 درجه بر دقیقه) کاهش ندهید.
7. با آب با کیفیت برای مدت 30 دقیقه در فشار خیلی کم (فشار بین غشایی کمتر از 25psi با حداکثر فشار تغذیه 45psi) شستشو دهید تا زهکشی شود.