جهت افزایش بهره وری از سیستم های اسمز معکوس، انواع مشخصی از مواد شیمیایی به ورودی این سیستم ها اضافه می شوند. از جمله:
● اسیدها
● سدیم هیدروکسید
● مواد دکلره
● آنتی اسکالانت و پراکنده کننده ها
اسیدها
معمولا از میان اسیدها، هیدروکلریک (HCl) و یا اسید سولفوریک اسید جهت کاهش PH به ورودی سیستم اسمز معکوس تزریق می شود.
در اکثر موارد استفاده از سولفوریک اسید نسبت به هیدروکلریک اسید ارجحیت دارد و یکی از دلایل مهم آن مقرون به صرفه تر بودن آن است. علت دیگر این است که بعد از تزریق سولفوریک اسید بخار کمتری در محیط پخش می شود و این به آن معناست که ریسک زنگ زدگی تجهیزات پایین تر می آید. همچنین در مواردی استفاده از سولفوریک اسید ترجیح داده می شود چون ممبران های اسمز معکوس عملکرد بهتری در دفع سولفات نسبت به کلراید حاصل از واکنش ها دارند.
سولفوریک اسید با گرید فنی(درجه کافی و مناسب از خلوص) و بدون ماده افزودنی دیگر جهت استفاده واحدهای اسمز معکوس مناسب می باشد. محلول سولفوریک با درجه خلوص %20 و %93 در بازار موجود است. سولفوریک اسید %93 همچنین با نام محلول بومه °66 (Baume) شناخته می شود. هنگام استفاده از سولفوریک اسید %93 نکات ایمنی را رعایت کنید. هنگامی که محلول سولفوریک اسید %60 رقیق سازی می شود دمای محیط واکنش به 280 درجه فارنهایت (137 درجه سانتیگراد) می رسد. بنابرای وقتی از ماده ای با خلوص بالا استفاده می کنید، محلول را به آرامی به آب رقیق و در حال جوش حاصل از واکنش اضافه کرده تا از ایجاد حادثه جلوگیری کنید.
هنگامی که کنترل رسوبات سولفات کلسیم، سولفات باریم و سولفات استرانسیم مد نظر باشد هیدروکلریک اسید به عنوان راه حل در نظر گرفته می شود. سولفوریک اسید باعث افزایش یون های سولفات در آب ورودی سیستم های اسمز معکوس می شود که در نهایت منجر به ایجاد رسوبات حاوی سولفات خواهد شد.هیدروکلریک اسید با گرید فنی و بدون مواد افزودنی گزینه مناسبی برای کنترل این نوع از رسوبات می باشد. هیدروکلریک اسید معمولا با درجه خلوص % 30 تا % 37 عرضه می شود. بعضی اوقات این ترکیب با نام جوهر نمک یا موریاتیک اسید شناخته می شود.
هدف اصلی از کاهش PH در آب ورودی به سیستم اسمز معکوس، کاهش احتمال تشکیل رسوبات کربنات کلسیم بر روی غشا است که بر اساس شاخص لانژلیه (LSI) اندازه گیری می شود. شاخص لانژلیه روشی برای نشان دادن پتانسیل میزان رسوب و خوردگی در آبهای لب شور با TDS پایین بر اساس میزان اشباع کربنات کلسیم است. LSI در شیمی سیستم های اسمز معکوس برای تعیین میزان تشکیل رسوبات از اهمیت بالایی برخوردار است. آب هایی با LSI منفی آب هایی هستند که ایجاد رسوب نکرده اما باعث زنگ زدگی و خوردگی لوله های فلزی می شوند. در مقابل آب هایی با LSI مثبت خاصیت خوردگی نداشته اما باعث ایجاد رسوبات در تجهیزات می شوند.
شاخص LSI عدد حاصل از تفریق PH اندازه گیری شده هنگامی که کربنات کلسیم اشباع شده از میزان PH آب ورودی به سیستم اندازه گیری می باشد. با افزایش دمای محیط، میزان حلالیت کربنات کلسیم کاهش می یابد(رسوب بستن و آهکی شدن کف کتری یک مثال واضح است). هر چه میزان PH بالاتر باشد میزان غلظت کلسیم محلول هم بیشتر بوده که این خود به معنی ایجاد محیط قلیایی است.
با تزریق اسید(سولفوریک اسید و هیدروکلریک اسید) میزان شاخص LSI هم در سیستم غشای اسمز معکوس کاهش می یابد. LSI پیشنهادی در ممبران ها عدد منفی 0.2 می باشد. این عدد بدین معنی است که میزان PH در غشا به مقدار 0.2 واحد کمتر از هنگامی است که غلظت کربنات کلسیم به حالت اشباع می رسد و این عدد نشان می دهد که کربنات کلسیم به نقطه ای نرسیده که در تجهیزات رسوب کند. در نتیجه ی تزریق اسید و رسیدن شاخص LSI به عدد منفی دو، PH آب به طور موقت تغییر کرده و از ایجاد رسوب جلوگیری می کند. همچنین آنتی اسکالانت های پلیمری از ایجاد رسوبات کربنات کلسیم جلوگیری می کنند. برخی از تامین کنندگان آنتی اسکالانت گزارش داده اند که این ترکیبات در LSI 2.5 هم کارآمد بوده و از ایجاد رسوبات کربنات کلسیم جلوگیری کرده اند. این در حالی است که این عدد در تولید این ترکیبات 1.8 در نظر گرفته شده است.
اسیدها همچنین جهت نگهداری از بسترهای کربن فعال هم استفاده می شوند.معمولا کربن فعال فشرده به دلیل فاکتورهای اقتصادی صرفا در واحدهای تصفیه کوچک به کار می رود (سیستم هایی که میزان ورودی آنها از 50 -100 گالن در دقیقه کمتر باشد).استفاده از بسترهای کربن فعال مزایای خاص خود را دارد از جمله ۱) حذف مواد آلی از جریان ورودی که می تواند در ممبران ها رسوب کنند. ۲) این روش تصفیه در مقایسه با روش های شیمیایی می تواند طیف بیشتری از آب های ورودی به سیستم با کیفیت های مختلف را پوشش دهد.
توصیه می شود که از کربن فعال با درجه پرمیوم(درجه ای که مواد بهترین کیفیت را دارند) استفاده شود. این نوع از کربن های فعال با استفاده از اسید شستشو داده شده تا فلزات سنگین و عناصر سختی از آنها حذف شوند. همچنین اندازه حفره های آنها به نحوی است که رسوبات در آنها تجمع نکنند. هر موقع که بستر جدیدی از کربن فعال در سیستم قرار داده می شود بایستی عمل شستشوی بستر صورت بگیرد و این کار تا جایی ادامه پیدا کند که دیگر جریان آب خروجی در سیستم وجود نداشته باشد که این فرآیند می تواند از چند ساعت تا چند روز طول بکشد. کارتریج فیلتر کربن فعال ۵ میکرونی به دلیل سایز حفره های خود نمی تواند به طور کامل از ایجاد رسوبات بر روی غشاهای اسمز معکوس جلوگیری کند و بعضی از ذرات و ترکیبات از آن عبور می کنند.
کاستیک
هنگامی که برای بعضی ار فرآیندها نیاز است که PH محیط بالا برود، از طریق تزریق کاستیک هایی با خاصیت قلیایی می توان PH ورودی به سیستم اسمز معکوس را افزایش داد. کاستیک به هر نوع ماده شیمیایی گفته می شود که خاصیت زنگ زدگی، سوختن پوست و هر نوع اثر تخریبی بر محیط اطراف خود را دارد. کاستیک ها به دو دسته اسید ها و بازهای بسیار قوی تقسیم می شوند. از میان کاستیک های قلیایی، سدیم هیدروکسید(NaOH) با نام تجاری سود سوزآور جهت بالا بردن PH سیستم های اسمز معکوس مورد استفاده قرار می گیرد. این ماده به دلیل دسترسی آسان، حلالیت مناسب در آب و مقرون به صرفه بودن اولین انتخاب برای فرآیند ذکر شده می باشد.
در اکثر موارد کیفیت سدیم هیدروکسید در حد گرید فنی و عاری از هرگونه ماده افزودنی است. چنانچه سدیم هیدروکسید رنگ شفافی نداشته و برای مثال به رنگ برنزه مایل به سیاه باشد در آن صورت سدیم هیدروکسید با گرید فنی بالاتر از جمله گرید رابون و یا نایلون را می توان برای بهره وری بالاتر جایگزین کرد.( این گریدها کمیت هایی هستند که میزان خلوص و کیفیت هر ماده شیمیایی را نشان می دهند و هر چه یک ترکیب گرید بالاتری داشته باشد بدان معناست ناخالصی های کمتری دارد) . سدیم هیدروکسید %100 به صورت کریستال های سفید رنگ و خلوص %20 یا %50 آن به شکل مایع در دسترس می باشد. چنانچه قصد انبار کاستیک %50 را دارید، این نکته را در نظر داشته باشید که این محلول در دمای زیر 15.5 درجه سانتی گراد فریز می شود. با بالا رفتن PH، شاخص LSI هم افزایش یافته و میزان حلالیت آهن، منگنز و کلسیم کربنات کاهش می یابد و بایستی به این نکته نیز در حین فرآیند مذکور دقت کنید.
پروسه معمول استفاده از کاستیک در جریان ورودی شامل تزریق آن از دور دوم و تکرار دوباره این مرحله می باشد یعنی در کل ۲ بار تزریق و از دور دوم. در این فرایند، آب حاصل از دور اول برگشت داده شده و در دوم با تزریق کاستیک آب پیش تصفیه مجددا از غشا عبور داده می شود. این کار کمک می کند تا آب خامی که در در دور اول از سیستم عبور کرد از رسوبات پاک شده و آب به درجه خلوص MΩ-cm) 4) برسد. کاستیک سودا به ۴ دلیل در دور دوم به سیستم تزریق می شود:
● هنگامی که PH آب به عدد 8.5 یا بالاتر می رسد، همه گاز کربن دی اکسید به یون بیکربنات تبدیل می شود. یون بیکربنات از طریق ممبران از آب دفع می شود. از آنجایی که کربن دی اکسید به حالت گاز وجود دارد، در دور اول به راحتی از غشا عبور می کند و وجود این گاز در خروجی که به بستر رسوب زدایی منتقل می شود، نامطلوب است به همین دلیل در دور دوم که این گاز به یون بیکربنات تبدیل شده به راحتی از آب خروجی سیستم جدا می شود.
● کربن آلی کل (TOC) موجود در آب در محیط قلیایی بهتر حذف می شود.
● میزان حلالیت سیلیکات و دفع آن در PH های بالا و قلیایی بیشتر است(مخصوصا PH های بالاتر از 9). باید این نکته را بدانید که غشاهای اسمز معکوس قادر به جداسازی مواد و عناصر محلول از آب هستند.
● میزان دفع بور در PH های بالا و قلیایی بیشتر است(مخصوصا PH های بالاتر از 9)
با بالا رفتن قلیائیت آب، سیلیکا به حالت محلول درآمده و در عین حال از ایجاد رسوبات ارگانیک و آلی جلوگیری میشود.
آب تغذیه ای که وارد واحد تصفیه خانه می شود معمولا از لحاظ کیفی آب لب شور می باشد. این آب حاوی رسوباتی است که در PH های بالا مشکلات بیشتری ایجاد می کنند(مانند سختی، وجود آهن و منگنز و قلیائیت آب). در این مورد برای پیش تصفیه از نرم کننده های آب، فیلتراسیون، اسیدهای ضعیف، رزین کاتیونی و گاززدا استفاده می شود تا از ایجاد رسوب در سیستم جلوگیری شود.
جهت حذف کلسیم و منیزیم در پیش تصفیه از مواد نرم کننده ای مانند آهک سودا و سپس فیلتراسیون کمک گرفته می شود. رزین های کاتیونی ضعیف جهت حذف سختی آب وابسته به قلیایت به کار می روند. هیدروژن آزاد شده از این فرآیند با قلیای آب واکنش داده و کربنیک اسید را تولید می کند که در مرحله بعدی توسط گاززدایی حذف می شود. میزان رسوبات کلسیم و کربنات بعد از فرآیند پیش تصفیه به مقدار چشمگیری کاهش یافته و در نتیجه این امکان فراهم می آید تا ادامه عملیات تصفیه در PH های بالاتر صورت بگیرد.
ضدعفونی غشاها
جهت ضدعفونی و حذف آلودگی های بیولوژیکی در ممبران های اسمز معکوس از هیدروژن پروکساید و یا ترکیب آن با پراستیک اسید استفاده می شود. نتایج نشان داده که این فرآیند به خوبی در حذف آلودگی های بیولوژیکی بر روی غشاهای اسمز معکوس™FilmTec (از برند دوپونت) و نانوفیلتراسیون موفق عمل می کند. محلول هیدروژن پراکسید/ پراستیک اسید در غلظت بالا در بازار عرضه می شود که این ترکیب بایستی تا حدی با آب پیش تصفیه ترکیب شده تا این ترکیب به غلظت %0.1 برسد.
قبل از استفاده از این ترکیب برای ضدعفونی ممبران های اسمز معکوس بایستی این نکته مهم را مد نظر داشته باشید که دو عامل مهم دما و آهن در میزان آسیب هیدروژن پراکسید به غشاها تاثیر می گذارند.
دمای ممبران در هنگام شستشو با این ماده نباید بیشتر از 25 درجه سانتی گراد باشد. غشاهای FT30 که در دمای 34 درجه سانتی گراد با محلول هیدروژن پراکسید شستشو داده شده اند، بعد از چند ساعت میزان بالایی از نمک از این غشاها عبور کرده است که این خود نشان دهنده ی آسیب به ممبران هاست. این در حالی هست که شستشوی همین ممبران ها با هیدروژن پراکسید %0.5 در دمای 24 درجه سانتی گراد بعد از 96 ساعت بهره وری و سازگاری مناسبی را با این ترکیب نشان می دهد.
همچنین وجود آهن و سایر فلزات واسطه در کنار هیدروژن پراکسید باعث آسیب به ممبران ها می شود. برای آزمایش این مورد، غشای FT30 در تماس با هیدروژن پراکسید %0.15 همراه با آب لوله کشی که حاوی آهن است شستشو داده شد. بعد از 150 ساعت، میزان عبور نمک ها از غشا به طور چشمگیری افزایش پیدا کرد. در هر صورت، تماس مداوم با این ترکیب می تواند در نهایت باعث آسیب به غشا شود. به همین جهت توصیه می شود که این ترکیب را به صورت دوره ای استفاده کنید.
جهت ضدعفونی کردن غشاهای FT30 با استفاده از محلول هیدروژن پراکسید طبق دستورالعمل زیر اقدام کنید:
1. قبل از هرچیز، با استفاده از یک ترکیب قلیایی ممبران ها را شستشو داده تا هرگونه ماده باقی مانده بر روی غشاها را پاک کنید. میکروارگانیسم هایی که در لابه لای این رسوبات و مواد زندگی می کنند از طریق این فرایند از محیط پاک می شوند.
2. غشا را با استفاده از یک اسید مناسب شستشو داده تا مواد مضر بخصوص رسوبات آهن از روی ممبران ها پاک شوند. سپس با آب پیش تصفیه ممبران را شستشو دهید.
3. محلول %0.1 هیدروژن پراکسید را با آب پیش تصفیه رقیق کرده و در دمای زیر 25 درجه سانتی گراد به مدت 20 دقیقه در سیستم به گردش در آورید. PH در حدود 4-3 برای از بین بردن میکروارگانیسم ها بهترین بهره وری را دارد و همچنین به عمر بیشتر غشا کمک می کند.
4. توصیه می شود که فرآیند ضدعفونی غشاها را یک الی دو بار در هفته انجام دهید.
کاربرد دیگر ضدعفونی کننده ها در مورد بسترهای کربن فعال است. با تمام مزایایی که کربن فعال در فرایند پیش تصفیه آب های ورودی به سیستم های اسمز معکوس دارند، نکته منفی در مورد آنها ایجاد محیط مناسب و مغذی برای رشد باکتری ها که این خود مسبب ایجاد رسوبات بیولوژیکی در واحدهای تصفیه می شود. بررسی ها نشان داده که میزان باکتری هایی که بعد از ۲۴ ساعت بر روی بسترهای کربن فعال باقی می مانند در مقایسه با سایر موارد دو برابر بیشتر است. فرآیند ضدعفونی بسترها تنها راه حل برای رفع این مشکل می باشد. در صنعت داروسازی که سطح بالای بهداشت در واحدهای تولید از اهمیت بالایی برخوردار است، فرکانس ضدعفونی کردن بسترها در بین یک تا هفت روز متغیر می باشد.
شستشو غشا با مواد دکلره
هیچ وقت، هیچ مقداری از کلر آزاد نبایستی در جریان ورودی به غشاهای اسمز معکوس وجود داشته باشد. حتی کمترین مقداری از کلر باعث اکسید شدن و آسیب به غشاهای اسمز معکوس می شود. به همین دلیل اپراتورها همیشه بایستی مراقب بوده تا هیچ ماده اکسید کننده ای وارد سیستم نشود. دو روش معمول پیش تصفیه جهت حذف کلر، جذب آن توسط گرانول های کربن فعال و یا استفاده از مواد شیمیایی مانند سدیم بی سولفات می باشد.
معمولا از سدیم متابی سولفیت(SBS) برای واحدهای بزرگ اسمز معکوس جهت حذف عامل کلراسیون(ضدعفونی کننده ها) و مراقبت از غشاها استفاده می شود. این ترکیب بعد از فرآیند ضدعفونی به کار می رود تا از تجهیزات واحد تصفیه محافظت شود. البته این نکته مهم را در نظر داشته باشید که SBS همراه با کبالت کاتالیز شده باشد. محلول SBS از ترکیب سدیم متابی سولفیت جامد در آب بدست آمده و محلول %1 آن دارای PH حدود 4.6 و محلول %10 آن نیاز به اضافه کردن 231 گرم از SBS در یک گالون آب دارد. محلول سدیم متابی سولفیت با خلوص %95.7 و %99 در بازار موجود است و بدون ایجاد مشکلات ایمنی به راحتی بالای ۶ ماه در مکانی خشک می توان آن را نگهداری کرد. اما این ماده با اکسیژن و کلرید واکنش می دهد در نتیجه توصیه می شود که بسته ای SBS با غلظت %2 بین 3 تا 7 روز و محلول های %10 بین 7 تا 14 روز مورد استفاده قرار بگیرند. از لحاظ تئوری مقدار 1.47ppm از SBS( و یا مقدار 0.7ppm از سدیم متابی سولفیت) قادر است 1ppm کلرین را خنثی کند. طراحان جهت رعایت نکات ایمنی برای غشاهای اسمز معکوسی که با لب شور تغذیه می شود، مقدار 1.8ppm تا 3 از SBS را با 1ppm کلرین را برای شستشوی این ممبران ها در نظر گرفته اند. میزان تزریق این ترکیب به جریان بالادستی سیستم بایستی در حدی باشد که میزان زمان واکنش حداقل به 20 ثانیه برسد. همچنین ماده مدکور بایستی به خوبی با ورودی سیستم ترکیب شده و جریان یکدستی داشته باشد.
دکلره کردن با استفاده از SBS در مقایسه با کربن فعال در واحدهای تصفیه بزرگ، مقرون به صرفه تر بوده و نیاز به هزینه کمتری دارد و SBS باقیمانده و ترکیبات حاصل از فعل و انفعالات آن در سیستم از طریق ممبران ها دفع می شود. نکته منفی آن نیاز به آماده سازی و ساخت محلول با رقیق سازی کنترل شده است و چنانچه محلولی با غلظت مناسب ساخته نشود امکان دارد به اندازه کافی موثر نبوده و در نتیجه کلرین به درون غشا نفوذ کرده و باعث تخریب ممبران شود. از طرف دیگر چنانچه در اب باکتری های احیا کننده سولفات(SBRs) حضور داشته باشند، از بی سولفیت موجود در ترکیب به عنوان منبع تغذیه استفاده کرده و ایجاد کلونی و بیوفیلم می کنند.این گونه از باکتری ها معمولا در شرایط بی هوازی رشد کرده و معمولا هیدروژن سولفید هم در نتیجه متابولیسم های آن ها تولید می شود.
میزان کلر آزاد در محیط با دستگاههای مربوطه و یا با استفاده از دستگاه سنجش اکسایش آب (ORP) بررسی می شود. بهتر است که همیشه ورودی ممبران های اسمز معکوس و نانوفیلتراسیون به دستگاه اندازه گیری اکسایش آب (ORP) مجهز شود و آب ورودی به سیستم به طور مداوم با استفاده از دستگاه سنجش شود. اما در مورد فاضلاب که از کلرامین برای آن استفاده می شود عددی که دستگاه نشان می دهد بایستی کمتر از 300mV باشد. چنانچه دستگاه عددی بیشتر را نشان دهد، اپراتور بایستی بداند مواد اکسید کننده در جریان آب هست و ممبران ها آسیب پذیر و در معرض صدمه هستند. در این حالت بایستی اقدامات لازم از جمله اضافه کردن مقدار معینی از SBS انجام گرفته تا دوز اکسید کننده ها به حد امنی برسد. چنانچه این عدد به مقدار 350 برسد کل سیستم بایستی خاموش شده و تا زمانی که اکسیدکننده ها به حد مناسب برسند در همان حالت باقی بماند.
ممبران های CPA قدرت تحمل مقدار 2,000 - 1,000 ppm کلرین در هر ساعت را دارند. در صورتی که غلظت کلرین از این عدد تجاوز کند، میزان عبور نمک ها از غشا دو برابر خواهد شد. چنانچه این محدوده به طور مداوم رعایت شود این میزان کلرین تا سه سال هم آسیبی خاصی به ممبران ها نمی رساند. البته عوامل دیگری نیز در این محاسبه می توانند دخیل شوند از جمله دمای بالای 25 درجه سانتی گراُد، PH برابر یا بالاتر از 7 و وجود فلزات واسطه بخصوص آهن که نقش زیادی در اثر و نفوذ کلرین بر غشاها دارد. وجود هر کدام از این عوامل عمر غشاها را به طور چشمگیری پایین می آورد.
شرایط ذکر شده برای ممبران های CPA و قدرت تحمل آن ها در مواجه با ترکیب کلرآمین با دوز 200,00 - 50,000 ppm در هر ساعت صدق می کند. چنانچه این محدوده به طور مداوم رعایت شود این میزان کلرامین تا سه سال هم آسیبی خاصی به ممبران ها نمی رساند. البته عوامل دیگری نیز در این محاسبه می توانند دخیل شوند از جمله دمای بالای، PH پایین و وجود فلزات واسطه. هر کدام از این عوامل عمر غشاها را به طور چشمگیری پایین می آورد.
سنجش های مداوم از یک واحد تصفیه در کالیفرنیا نشان داده که میزان دفع نمک ها بعد از دو تا سه سال مواجه غشاها به دوز 6-8 ppm کلرامین، از %98 به %96 کاهش پیدا کرده است.
کلرامین از ترکیب کلرید و آمونیاک تولید می شود. کلرین آزاد نسبت کلرامین به مقدار بیشتر و سریع تری غشاها را تخریب میکند و این اتفاق هنگامی می افتد که مقدار کافی آمونیا جهت حذف کلرین آزاد استفاده نشده و مقداری کلرین آزاد بر روی غشا باقی می ماند. به همین دلیل بسیار مهم است که همیشه مقداری آمونیاک اضافه در سیستم وجود داشته باشد و شرایط به طور مداوم کنترل شود.
آنتی اسکالانت ها و پراکنده کننده ها
آنتی اسکالانت ها گروهی از مواد شیمیایی هستند که جهت جلوگیری از تشکیل رسوبات و نمک های کریستالی مواد معدنی طراحی و تولید شده اند. بیشتر آنتی اسکالانت ها پلیمرهای مصنوعی ساخته شده دست انسان هستند و به طور طبیعی وجود ندارند. پلی اکریلیک اسید، کربوکسیلیک اسید، پلی مالیک اسید، ارگانوفسفات، پلیمرهای آنیونی و … نمونه هایی از این ترکیبات می باشند.
نیاز به وجود تولید آنتی اسکالانت ها در ابتدا در صنایعی احساس شد که از سیستم های خنک کننده و دیگ های بخار آب استفاده می کردند و در ابتدا ترکیبات مذکور برای این منظور تولید شدند و از آن هنگام انواع و اقسام آنتی اسکالانت ها برای صنایع و اهداف مختلف تولید و به بازار عرضه شد.
استفاده از آنتی اسکالانت هایی که ساختار آنها از پلی آکریلیک اسید است نیاز به مراقبت های ویژه دارد. به نظر میآید که این دسته از آنتی اسکالانت ها در حضور میزان بالای آهن باعث ایجاد رسوبات بر روی ممبران ها می شوند. حضور این رسوبات بر روی ممبران ها منجر به افزایش فشار مورد نیاز جهت انجام فرآیند می شود. اما از طرفی می توان این رسوبات را با استفاده از محلول های مناسب با PH پایین حذف کرد.
همچنین بایستی در استفاده از آنتی اسکالانت هایی مانند پلی آکریلیک اسید که خاصیت آنیونی دارند نیز مراقب بود. هنگامی که یک منعقدکننده کاتیونی در مرحله پیش تصفیه مورد استفاده قرار می گیرد می تواند با این آنتی اسکالانت ها واکنش داده و رسوباتی را بر روی غشاها تولید کند که پاک کردن آن ها از سیستم بسیار مشکل خواهد بود.
آنتی اسکالانت هگزا متا فسفات سدیم (SHMP) آنتی اسکالانتی است که در ابتدا برای استفاده از غشاهای اسمز معکوس بسیار محبوب بود. اما با ظهور آنتی اسکالانت های مختلف و تخصصی تر میزان استفاده از این ماده شیمیایی به طور چشمگیری کاهش پیدا کرد. دلیل مهم آن این است که استفاده از این ترکیب محدودیت هایی دارد. بسته های رقیق شده این ماده بایستی هر دو تا سه روز ساخته شوند چون SHMP در تماس با هوا هیدرولیز و تجزیه می شود. این موضوع میزان اثرگذاری ماده مذکور را کاهش داده و ریسک تشکیل رسوبات کربنات کلسیم بر روی ممبران ها بالا می رود. همچنین با افزایش حداکثری LSI در غلظت 1.0+ میزان اثرگذاری این ماده برای جلوگیری از تشکیل رسوبات کربنات کلسیم کاهش پیدا می کند.
همانطور که ذکر شد آنتی اسکالانت ها از تشکیل کریستال های نمک در آب ورودی به سیستم های اسمز معکوس جلوگیری می کنند. آنتی اسکالانت ها می توانند در کنار اسید ها و یا به جای اسیدها برای حذف و جلوگیری از رسوبات نمکی مورد استفاده قرار بگیرند.
میزان تشکیل رسوبات به فاکتورهایی در محیط بستگی دارد که ما در اینجا به آن اشاره میکنیم. کاهش دما میزان حلالیت رسوبات معدنی را کاهش می دهد. البته در اینجا کربنات کلسیم یک استثناست و با افزایش دما میزان رسوبات این ماده در آب افزایش می یابد. با افزایش TDS (کل جامدات محلول در آب) یون های موجود در آب تماس بیشتری با هم پیدا کرده و این موضوع منجر به تشکیل رسوبات بیشتری در آب می شود.
رسوبات معمول در آب که مشکلاتی را در واحدهای تصفیه ایجاد می کنند شامل:
● کربنات کلسیم [CaCO3]
● سولفات کلسیم [CaSO4]
● سولفات استرانسیوم [SrSO4]
● سولفات باریم [BaSO4]
و رسوباتی که کمتر معمول بوده شامل:
● فسفات کلسیم [CaPO4]
● کلسیم فلوراید [CaF2]
پراکنده کننده ها دسته ای از مواد آلی مصنوعی و ساخته شده هستند که مواد معلق معدنی را پراکنده کرده و از تجمع این مواد بر روی سطح غشاهای اسمز معکوس جلوگیری می کنند. گاهی پراکنده کننده ها به عنوان ضد رسوب شناخته می شوند. مواد معلق در مقایسه با رسوبات موادی نرم تر و غیر کریستالی هستند در حالی که رسوبات ساختاری سخت تر و کریستالی دارند. پراکنده کننده ها معمولا خاصیت ضد رسوبی دارند. اثربخشی هر کدام از آنها بستگی به این دارد که با چه ترکیب شیمیایی مواجه شوند.
مواد معلقی که با استفاده از پراکنده کننده ها تصفیه می شوند شامل:
● رسوبات معدنی
● اکسید و هیدروکسید فلزات (آهن، منگنز و آلومینیوم)
● سیلیکای پلیمری
● مواد کلوئیدی (ذرات بسیار ریزی که به صورت معلق در آب هستند و از خاک رس، آهن، آلومینیوم، سیلیکا، گوگرد و مواد آلی تشکیل شده اند.
● مواد آلی
پیش بینی حداکثر مقدار حلالیت سیلیکا در یک محلول فوق اشباع می تواند مشکل باشد. بخصوص اینکه آهن موجود در آب تغذیه و ورودی به سیستم می تواند تشکیل سیلیکات آهن داده و به طور چشمگیری میزان غلظت سیلیکای مجاز ورودی به سیستم اسمز معکوس را کاهش دهد. سایر فاکتورها همچون دما و PH نیز در این مقدار دخیل هستند.
پیش بینی میزان حداکثر فلزات ( مانند آهن، منگنز، آلومینیوم) نیز می تواند مشکل باشد. نوع محلول یون های فلزی امکان اشباع بیشتری را فراهم می آورد. نوع غیر محلول فلزات معمولا خودش را به صورت ذرات معلق و کلوئیدی نشان می دهد.
بهترین مرجع برای تعیین میزان مجاز اشباع رسوبات و مواد معلق برای استفاده از آنتی اسکالانت ها و پراکنده کننده ها همان کارخانه های تولیدی این محصولات می باشند که با توجه به دستورالعمل آن ها می توان به این مقدار پی برد. این واحدهای تولیدی از نرم افزارهای مخصوصی مانند Wave، Winflow، ROSA ، IMSDesign(نرم افزارهای طراحی و آنالیز سیستم آب شیرین کن) برای تعیین دوزها استفاده می کنند. این نرم افزارها با محاسبات خاص میزان بیش از حد مجاز ترکیبات مضر موجود در سیستم را تشخیص داده و وجود آن ها را هشدار می دهند.
تنظیم میزان مناسب دوز آنتی اسکالانت ها و پراکنده کننده ها در سیستم مهم است. میزان کم این ترکیبات تاثیر کافی بر رسوبات را نخواهد داشت که این موضوع منجر به تشکیل رسوبات در واحدهای تصفیه می شود. از طرف دیگر میزان بالای آن ها روی غشاهای اسمز معکوس ته نشین شده و منجر به ایجاد گرفتگی در غشاها می شوند. به همین جهت،شستشوی کامل این ترکیبات بعد از استفاده و خاموش کردن سیستم از اهمیت بالایی برخوردار است. تزریق آنتی اسکالانت و پراکنده کننده ها هنگامی که فشار آب شستشو در سیستم پایین بوده و ورودی به سیستم صرفا آب تفدیه است بایستی متوقف شود. به دلیل اینکه در فشار پایین دبی آب کم است و در نتیجه این مواد به خوبی با آب ترکیب نمی شوند. این موضوع باعث بالاتر رفتن غلظت مواد در یک جا و بی اثر بودن آنها در نقطه ای دیگر می شوند و به این ترتیب احتمال تشکیل رسوبات در سیستم افزایش پیدا می کند.
مخلوط شدن مناسب این نوع از ترکیبات در آب از اهمیت بالای برخوردار است. استفاده از یک دستگاه مناسب برای این منظور می تواند از ایجاد بسیاری از این مشکلات جلوگیری کند. اما از آنجایی که این روش هزینه بر است بیشتر سیستم های اسمز معکوس، یک نقطه تزریق درست قبل از فیلتر کارتریج در نظر گرفته و با بهره گرفتن از زمان گذر از فیلتر کارتریج یک ترکیب یکدست در آب ورودی به سیستم را ایجاد می کنند.
چنانچه فرآیند تصفیه نیاز به تزریق اسید داشته باشد، توصیه می شود که این کار در جریان بالادستی انجام گرفته تا قبل از رسیدن به نقطه مخصوص تزریق آنتی اسکالانت و پراکنده کننده ها به خوبی در آب پخش شده باشد. در غیر این صورت جمع شدن اسیدها در یک نقطه مشخص، میزان PH آن نقطه را پایین آورده و باعث بی اثر شدن آنتی اسکالانت ها و پراکنده کننده ها می شود.
پمپ تزریقی که برای افزودن آنتی اسکالانت ها و پراکنده کننده ها مورد استفاده قرار می گیرد بایستی در حداکثر فرکانس تزریق تنظیم شود. حداقل میزان تکرار تزریق قابل قبول برای افزودن این مواد هر پنج ثانیه یکبار می باشد.
آنتی اسکالانت ها و پراکنده کننده ها به دو شکل مایع و یا پودری عرضه می شوند. همچنین بهتر است آبی که با این مواد ترکیب می شود از آب پیش تصفیه و فاقد عوامل سختی باشند. چنانچه این آب در تانکی نگهداری شود با توجه به دما بعد از حدود بیست و چهار ساعت شروع به تشکیل رسوبات بیولوژیکی میکند به همین دلیل پیشنهاد می شود که ترکیب رقیق شده با آب بیشتر از 10-7 روز نگهداری نشود.
جدول زیر حداکثر میزان اشباع توصیه شده از عوامل رسوبات مختلف را در آب ورودی به سیستم اسمز معکوس نشان می دهد. به معنای دیگر عددی بالاتر از این مقدار باعث ایجاد هشدار در سیستم های تحت کنترل خواهد شد.
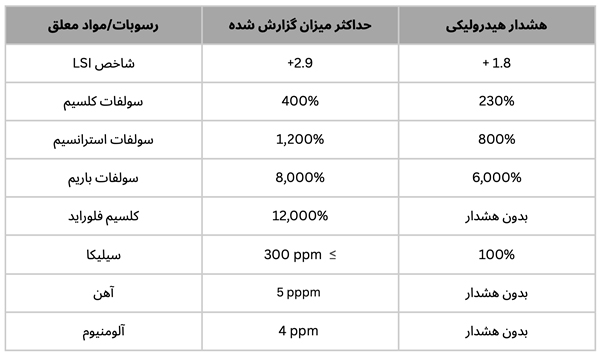
نکته ای دیگری که در هنگام انتخاب آنتی اسکالانت و پراکنده کننده ها بایستی در نظر گرفته شود این است که این مواد شیمیایی با ساختار غشاهای به کار رفته در واحد تصفیه خانه مطابقت داشته باشند. عدم سازگاری مواد شیمیایی با ساختار و شیمی ممبران منجر به ایجاد رسوب و یا حتی آسیب به آن ها شود.
بنابراین در هنگام خرید این مواد شیمیایی بهتر است این سوالات را از فروشنده بپرسید:
● آیا این ماده با مدل ممبران من سازگاری دارد؟
● آیا نتایجی از بررسی و تحقیق در مورد عملکرد این مواد و تاثیرات آن ها با بیش از 1000 ساعت عملیات موفق وجود دارد؟
● آیا این مواد به سایر ترکیبات موجود در آب ورودی مانند آهن و فلزات سنگین حساس است؟
● میزان توصیه شده و حداکثر دوز تزریقی آن چقدر است؟
● محدوده فرض شده برای حلالیت و رسوب هر کدام از ترکیبات در آب چیست؟
● آیا خطر خاصی در صورت نشتی مواد وجود دارد؟
● آیا این ترکیبات در صورت نیاز برای تصفیه آب شهری مناسب هستند؟
● آیا فروشنده در کنار این محصولات، منعقد کننده های سازگار با این آنتی اسکالانت ها را پیشنهاد می دهد؟
● آیا عرضه کننده محصولات، خدماتی همچون بررسی ساختار ممبران ها و یا تمیز کردن آن ها را ارائه می دهد؟
اصطلاحات
مقیاس PH: برای بیان حالت بازی یا قلیایی بودن یک ماده به کار می رود. چنانچه PH برابر عدد 7 باشد آن ماده یا ترکیب خنثی در نظر گرفته می شود. عدد بالاتر از 7 و تا میزان 14 نشان دهنده ی خاصیت قلیایی و برعکس عددهای پایین تر از 7 تا عدد 0 نشان دهنده ی خاصیت های اسیدی است. این مقیاس در واقع به نحوی بیانگر غلظت اتم هیدروژن می باشد. از نظر شیمی آب، میزان شاخص PH آب برای بیان ویژگی قلیائیت و حضور عوامل آن از جمله کربن دی اکسید، کربنات، بیکربنات و یون هیدروکسید اهمیت دارد. غلظت این عوامل در آب و نسبت آنها با یکدیگر در مراحل مختلف تصفیه با هم متفاوت است. نرم افزارهای طراحی و تحلیل سیستم اسمز معکوس می تواند به کارشناسان کمک کنند که برای تنظیم مناسب PH دقیقا چه مقدار از اسیدهایی مانند سولفوریک اسید و هیدروکلریک اسید در آب ورودی به سیستم استفاده کنند. کاهش PH آب تغذیه به معنای کاهش شاخص LSI می باشد. پایین بودن عدد LSI نشان می دهد که آب دیگر خاصیت ایجاد رسوب کلسیم کربنات در سیستم و تجهیزات را ندارد. میزان PH و شاخص LSI آب ورودی و پساب همچنین در میزان دفع یون های موجود در آب و پتانسیل رسوبات دیگر مانند سیلیکا، آلومینیوم، مواد معدنی و چربی ها نیز موثر است. برای مثال هنگامی که PH آب پایین بوده و خاصیت اسیدی داشته باشد، میزان دفع ترکیباتی مانند فلوراید، بر و سیلیکا هم کمتر می شود.
قلیائیت: این اصطلاح در درجه اول به ترکیباتی از جمله کربن دی اکسید، بیکربنات، کربنات و هیدروکسید اشاره دارد. قلیائیت در آب با توجه به PH های مختلف با ترکیبات خاصی خود را نشان می دهد. طبیعت یک سیستم بافری بزرگ است. هنگامی که PH طبیعت به دلیل وقایع مختلف مانند باران های اسیدی دستخوش تغییر میشود، طبیعت با سیستم بافری خود توازن را برقرار می کند. در PH های بین 8.2 - 4.4 کربن دی اکسید و بیکربنات در توازن هستند. هنگامی که PH به 4.4 یا پایین تر می رسد، تمام قلیائیت به شکل کربن دی اکسید وجود دارد. هنگامی که PH محیط به 8.2 می رسد تمام قلیائیت به شکل بیکربنات است و اصلا دی اکسید کربن وجود ندارد. در PH های 9.6 - 8.2 کربنات و بیکربنات در توازن هستند. در PH 9.6 هیچ کربن دی اکسید و بیکربناتی وجود ندارد و تمام قلیائیت به شکل کربنات است. در PH های بالای 9.6 به دلیل وجود یون هیدروکسید قلیائیت هیدروکسیلی رخ می دهد.بیشتر منابع طبیعی دارای PH بین 8.4 - 6 هستند و وجود هیدروکسید در منابع آب نشان از فعالیت های انسانی دارد. قلیائیت آبهای دیگ های جوش در صنعت با دو اصطلاح P-Alkalinity و M-Alkalinity اندازه گیری و سنجش می شود. M-Alkalinity میزان کل قلیائیت در آب را برحسب کلسیم کربنات به ppm نشان می دهد در حالی که P-Alkalinity مقدار قلیائیت را بر اساس بی کربنات، کربنات و هیدروکسیل نشان می دهد. میزان هر کدام از ترکیبات با کمک آزمایش تیتراسیون و نشانگرهای مخصوص تعیین می شود. برای مثال برای M-Alkalinity از Methyl نارنجی تا رسیدن PH به مقدار 4.2 و برای M-Alkalinity از نشانگر Phenolphthalein صورتی تا رسیدن به PH به عدد 8.2 استفاده می شود. جدول زیر نوع قلیائیت آب در PH های مختلف را نشان می دهد:
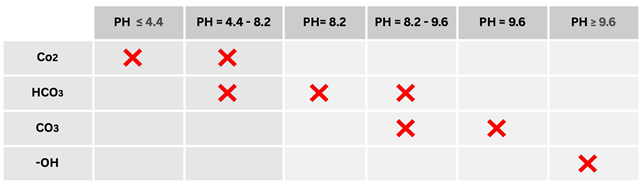
شاخص SDSI:( مخفف اصطلاح Stiff-Davis Saturation Index) این شاخص نیز مانند شاخص LSI برای نشان دادن پتانسیل ایجاد رسوب یا خوردگی بر اساس میزان اشباع کربنات کلسیم به کار می رود. شاخص SDSI برای نشان دادن خصوصیات آب های شور دریا با TDS بالا به کار می رود در حالی که شاخص LSI مختص آب لب شور با TDS پایین است. دلیل استفاده از دو شاخص متفاوت برای این دو نوع آب به تاثیر قدرت یونی بر میزان حلالیت مواد برمیگردد. قدرت یونی و میزان حلالیت یک ماده با هم رابطه مستقیم دارند. هر چه میزان قدرت یونی بیشتر باشد میزان حلالیت آن ماده هم بیشتر است. در نتیجه چنانچه میزان TDS افزایش پیدا کند بدین معنی است که قدرت یونی کل آن ماده هم بالا می رود و در نتیجه حلالیت هم بیشتر می شود.
قدرت یونی: میزان حلالیت نمک های محلول در آب با افزایش TDS(کل ذرات محلول) هم زیاد می شود. بنابراین از قدرت یونی آب برای محاسبه میزان حلالیت نمک ها مانند سولفات کلسیم، سولفات باریم، سولفات استرانسیوم و همچنین شاخص SDSI استفاده می شود. برای محاسبه قدرت یونی به اندازه غلظت 1 ppm (با مرجع کربنات کلسیم) در نظر گرفته شده و هر یون تک ظرفیتی در 10-5×1 و هر یون دو ظرفیتی در 10-5×2 ضرب می شود. محاسبه قدرت یونی هر کدام از ترکیبات موجود و جمع آنها با هم در نهایت قدرت یونی آب را به ما نشان می دهد.
کربن دی اکسید(CO2): کربن دی اکسید در حالت طبیعی به شکل گاز وجود دارد و وقتی با آب واکنش میدهد به شکل یک اسید ضعیف با نام کربنیک اسید(H2CO) ظاهر می شود. در حالتی که آب خالص به طور کامل با کربن دی اکسید اشباع شود غلظت آن در این ترکیب در حدود ppm 1600 و PH در حدود 4 می باشد. مقدار کربن دی اکسید در طبیعت به میزان توازن آن با قلیائیت بیکربنات و PH آب بستگی دارد. غلظت کربن دی اکسید به طور غیر مستقیم با استفاده از مقایسه دیاگرام غلظت بی کربنات و PH محاسبه می شود.هنگامی که PH آب 4.4 باشد، تمام قلیائیت از کربن دی اکسید و هنگامی که PH برابر 8.2 باشد تمام قلیائیت مربوط به بیکربنات است . میزان غلظت یون بی کربنات و کربن دی اکسید در PH های بین این دو عدد در توازن است. طراحان سیستم های اسمز معکوس میزان غلظت کربن دی اکسید را سطح بیکربنات و میزان PH محاسبه می کنند. گاز کربن دی اکسید در سیستم اسمز معکوس نه دفع شده و نه در جایی جمع شده و رسوب می کند بنابراین غلظت آن در آب خام ورودی، پیش تصفیه و پساب به یک اندازه خواهد بود. افزودن اسید به آب و کاهش PH باعث تبدیل بیکربنات به گاز دی اکسید کربن خواهد شد.
بیکربنات (HCO3): یک آنیون تک ظرفیتی است. میزان حلالیت کلسیم بیکربنات در آب پایین است و می تواند باعث ایجاد رسوب در غشاهای اسمز معکوس شود. میزان حلالیت این ماده در آب های لب شور با استفاده از شاخص LSI و برای آب های دریا با کمک شاخص (SDI (Stiff-Davis Index اندازه گیری و نشان داده می شود. میزان حلالیت بیکربنات با افزایش دما و PH کاهش می یابد. بیکربنات یکی از عوامل قلیاییت است که غلظت آن در PH های بین 8.2 - 4.4 با غلظت کربن دی اکسید در توازن است و میزان آن با کربنات در طیف PH های 9.6 - 8.2 در توازن می باشد.
کربنات (CO3): یک آنیون دو ظرفیتی است و میزان حلالیت آن در آب پایین بوده و می تواند باعث رسوب در غشاهای اسمز معکوس شود. برای آبهای لب شور میزان حلالیت کربنات بر اساس شاخص LSI و برای آب دریا میزان آن براساس شاخص SDSI محاسبه می شود. میزان حلالیت این ماده با افزایش PH و افزایش دما کمتر می شود. همانطور که اشاره شد کربنات یکی از عوامل قلیائیت است و غلظت آن در PH های بین 9.8 - 8.2 با بیکربنات در توازن است. هنگامی که PH محیط به عدد 9.6 یا بالاتر می رسد، دیگر هیچ دی اکسید کربن و بیکربناتی وجود ندارد و همه قلیائیت به شکل کربنات است.
کلسیم(Ca): یک کاتیون دو ظرفیتی است. عنصر کلسیم به همراه منیزیم دو عامل بسیار مهم ایجاد سختی آب می باشند. مقدار حلالیت سولفات کلسیم (CaSO4) با استفاده از یک آنتی اسکالانت می تواند به %230 و میزان حلالیت آن بر اساس شاخص LSI بین 1.8 تا 2.5 محدود می شود.
باریم: یک کاتیون دو ظرفیتی است. میزان حلالیت سولفات باریم (BaSO4) پایین است و می تواند منجر به ایجاد رسوبات بر روی سطح ممبران های اسمز معکوس شود. مقدار حلالیت این ترکیب با کاهش دما و افزایش غلظت سولفات کمتر هم می شود. به طور معمول غلظت باریم در چاه های آب کمتر از 0.2 - 0.05 می باشد. اندازه گیری میزان باریم بایستی با دستگاه هایی انجام گیرد که قادرند ppm 0.01 را اندازه گیری کنند. به طور معمول آنتی اسکالانت ها نقطه اشباع این ترکیب را به %100 و فوق اشباع %6000 محدود میکنند.
آهن (Fe): به عنوان یک آلوده کننده آب شناخته می شود و به دو شکل اصلی در آب وجود دارد. فرم محلول آن دارای دو ظرفیت برای ایجاد پیوند است و تحت عنوان حالت فروس یا آهنی شناخته می شود. در چاه هایی که شرایط بی هوازی حاکم است، یون آهن بسیار شبیه به یون های کلسیم و منیزیم رفتار کرده و باعث سختی آب شده و میتوان آن را به کمک نرم کننده های مخصوص حذف کرده و یا به کمک پراکنده کننده ها در ممبران های اسمز معکوس در آب ورودی به سیستم کنترل کرد. نوع غیر محلول آن آهن فریک نامیده می شود و دارای سه ظرفیت پیوند می باشد. تولید کنندگان ممبران های اسمز معکوس توصیه می کنند که مقدار هر دو حالت آهن در حد 0.05 ppm در آب تغذیه نگه داشته شود چنانچه تمام آهن موجود در آب به حالت محلول و PH هم کمتر از 7 باشد، در آن صورت وجود آهن تا غلظت 0.5 ppm هم در آب مشکلی ایجاد نمی کند.(برای اطمینان بهتر است از پراکنده کننده استفاده شود.) هنگامی که آب هایی با محیط بی هوازی در معرض هوا قرار می گیرند نوع محلول آهن به حالت غیر محلول در می آید که همین موضوع منجر به ایجاد مشکلات بیشتری می شود. معمولا در چاه های عمیق آب نوع محلول آهن بیشتر وجود دارد هنگامی که این آب ها برای ذخیره به تانک ها منتقل شده یا در لوله های آسیب دیده جریان پیدا می کنند در معرض هوا قرار گرفته و آهن های نامحلول در آب تولید میشود. آهن محلول از طریق پراکنده کننده ها، نرم کننده ها، فیلترها و یا با استفاده از منعقد کننده ای مانند آهک از آب حذف و یا کنترل می شود. نوع غیر محلول آهن به شکل هیدروکسید آهن و به حالت کلوئیدی در طبیعت وجود دارد و در صورت ورود به سیستم غشایی ایجاد رسوب می کند. منابع آهن غیر محلول چاه های کم عمق و هوازی، آب های سطحی و تانک ها و لوله های آب می باشد. آهن غیر محلول از طریق فیلترهای آهن و اولترافیلتراسیون(با محدودیت)، آهک، نرم کننده های و فیلترهای چند لایه پلی الکترولیت حذف می شوند. نکات ایمنی جهت استفاده از پتاسیم پرمنگنات بایستی رعایت شود. این ماده در فیلترهای آهن وجود دارد و خاصیت اکسیدی داشته و می تواند به غشاهای پلی آمیدی آسیب برساند. همچنین در استفاده از پلی الکترولیت های کاتیونی نیز بایستی احتیاط کرد چرا که می توانند باعث ایجاد رسوبات دارای بار منفی شده و آسیب های غیرقابل برگشتی را به غشاهای پلی آمیدی وارد کنند. برای حفاظت تجهیزات از زنگ زدگی، استفاده از لوله های ضد زنگ مانند FRP ،PVC و لوله ای فولادی ضد زنگ برای تمام واحدهای تصفیه با اسمز معکوس، واحدهای پیش تصفیه و لوله های توزیع توصیه می شود. رسوبات آهن به سرعت میزان فشار مورد نیاز در واحد تصفیه را افزایش داده و همچنین باعث بالا رفتن میزان TDS آب میشوند. در بعضی موارد، رسوبات آهن منبع انرژی باکتری های اکسید کننده شده که منجر به ایجاد لایه لزج بیوفیلم و گرفتگی در تجهیزات می شود.
منیزیم (MG): یک کاتیون دو ظرفیتی است. این عنصر به عنوان سومین عامل مهم ایجاد سختی در آب های لب شور شناخته می شود در حالی که غلظت آن در آب دریا پنج برابر بیشتر از غلظت کلسیم است. میزان حلالیت این ماده بالاست و به همین دلیل معمولا مشکل خاصی در سیستم های اسمز معکوس ایجاد نمی کند.
منگنز (MN): منگنز عامل آلوده کننده آب است که هم در آب های سطحی و هم آب های چاه با غلظت بالای 3 ppm وجود دارد. منگنز مانند آهن به عنوان بخشی از مواد آلی پیچیده موجود در آب های سطحی وجود دارد. در آب های بی هوازی به صورت محلول و در آب های در معرض هوا و خاصیت اکسید کنندگی به حالت غیر محلول و معمولا به صورت منگنز اکسید سیاه (MnO2) یافت می شود. چنانچه میزان غلظت منگنز در آب ورودی و هوادهی شده در سیستم اسمز معکوس از 0.05 ppm بالاتر رود باعث ایجاد رسوب در تجهیزات و ممبران ها می شود. علاوه بر این وجود این مقدار از منگنز در آب منجر به ایجاد لکه های سیاه بر روی سطوح خواهد شد به همین دلیل بر اساس استانداردهای آب لوله کشی، غلظت منگنز در آب نباید از 0.05 ppm تجاوز کند. معمولا از پراکنده کننده ها جهت کنترل و پیشگیری از تشکیل رسوبات منگنز در واحدهای تصفیه استفاده می شود.
سیسلیکا (SiO2): سیلیکا یا سیلیکون دی اکسید بعضی اوقات به عنوان یک آنیون رفتار می کند. شیمی سیلیکا کمی پیچیده بوده و نوع واکنشی که انجام می دهد تا حدودی غیر قابل پیش بینی است. همچون شاخص TOC که میزان کل کربن ارگانیک را نشان می دهد بدون اینکه به ترکیب مشخصی اشاره داشته باشد، مقدار کل سیلیکون بدون اشاره به هیچ ترکیب خاصی صرفا با استفاده از سیلیکا نشان داده می شد. مقدار کل سیلیکای موجود در آب شامل سیلیکای واکنشی و غیر واکنشی است. سیلیکای واکنش پذیر(برای مثال سیلیکات SiO4) محلول است و به آرامی یونیزه شده و در ترکیباتی با زنجیره های طولانی قرار نمی گیرد. ای دسته از سیلیکا نوع مناسبی برای سیستم های غشاهای اسمز معکوس است و به نحوی در فرایندها از آن استفاده می شود. سیلیکای واکنش پذیر خاصیت آنیونی دارد اما نه به طوری که به عنوان عامل توازن در آب شناخته شود بلکه صرفا به عنوان بخشی از TDS آب بشمار می رود. نوع غیر محلول سیلیکا واکنش پذیر نبوده و در ساختارهای پلیمری و کلوئیدی مشارکت می کند. این نوع از سیلیکا دارای پتانسیل ایجاد رسوب در ممبران های اسمز معکوس است. ذرات کلوئیدی سیلیکا با اندازه بین - 0.45 0.0008 میکرون به عنوان تعیین شاخص SDI به کار می روند. دانه هایی مانند خاک رس، شن و ماسه که حاوی سیلیکا هستند معمولا دراتی بزرگتر از 1 میکرون بوده و در شاخص SDI مد نظر قرار می گیرند. سیلیکاهای پلیمری که ساختار آن ها از سیلیکون دی اکسید ساخته شده است در طبیعت به شکل سنگ های کوارتز و عقیق وجود دارند. همچنین سیلیکای پلیمری میتواند حاصل اشباع نوع واکنش پذیر و محلول آن باشد. نقطه اشباع سیلیکای محلول با کمک پراکنده کننده ها به % 300 - 200 محدود می شود. میزان حلالیت سیلیکا با افزایش دما بیشتر می شود. میزان حلالیت سیلیکا علاوه بر دما به PH محیط هم بستگی دارد و میزان حلالیت آن در PH های زیر 7 و بالای 7.8 با افزایش دما بیشتر می شود. عامل دیگری که در میزان حلالیت سیلیکا تاثیر می گذارد حضور آهن می باشد. آهن به عنوان کاتالیست برای تشکیل پلیمرهای سیلیکا عمل کرده و باعث کاهش حلالیت آن می شود. میزان دفع سیلیکا در ممبران های اسمز معکوس وابسته به PH آب است. چنانچه محیط قلیایی باشد میزان دفع سیلیکا به حالت واکنش پذیر و محلول آن نسبت به محیط های اسیدی بیشتر است.
استرانسیوم (Sr): یک کاتیون دو ظرفیتی است. میزان حلالیت سولفات استرانسیوم کم است و باعث ایجاد رسوب در ممبران های اسمز معکوس می شود. میزان حلالیت سولفات استرانسیوم با کاهش دما و افزایش غلظت استرانسیوم کمتر میشود. معمولا استرانسیوم در آب های چاهی که حاوی سنگ معدن هستند یافت می شود. سیلیکا با کمک آنتی اسکالانت ها، در غلظت کمتر از 15 ppm، نقطه اشباع %100 و نقطه فوق اشباع %800 خواهد داشت.
سولفات (SO4) : یک آنیون دو ظرفیتی است. میزان حلالیت سولفات کلسیم، سولفات باریم و سولفات استرانسیوم پایین است و می توانند باعث ایجاد رسوبات در غشاهای اسمز معکوس شوند. میزان حلالیت این نمک ها با کاهش دما هم کمتر می شود. میزان توصیه شده سولفات در آب های لوله کشی برای حفظ مزه مناسب آب کمتر از 250 ppm می باشد.